Humanity can only maintain an environment worth living in if we effectively reduce the consumption of resources. In recent years, the focus has primarily been on energy efficiency in building operation and CO2 emissions during production. Today, an ecological building is defined more by the quality of the building fabric. The origin of the raw materials, transportation routes, durability and recycling play a key role here. Sustainable building is always a triad of ecology, economy and socioculture. However, there is a fourth dimension of sustainability that no other building material for facades fulfills in the same way as clinker brick: aesthetic sustainability.
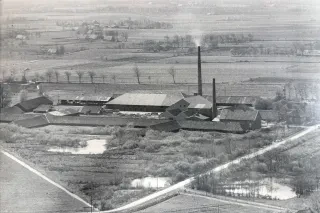
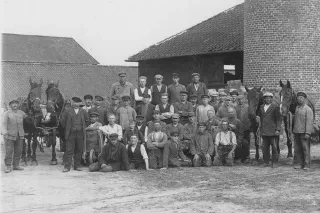
Resource-conserving extraction: clay on the doorstep
When raw materials travel, their ecological balance deteriorates with every kilometer they travel. We have no problem with this in Wittmund, as it is only about five kilometers from the clay pits to the plant. No trees have to be felled for clinker production, clay pits are limited areas and the resources are practically inexhaustible. A renaturation plan is drawn up for each clay pit as early as the extraction permit stage. Once a clay pit has been decommissioned, habitats for animals and plants are created that would not have existed without the previous extraction of clay.
Biologist Norbert Graefe, responsible for the ecological monitoring of the clay pits at Wittmunder Klinkerwerke in Spekendorf, explains how nature develops after use.
Regionalität
Wir sind in der Region verwurzelt.
Auch die Basis für unsere Klinker ist auch nach vielen Jahrzehnten noch dieselbe: Die Abbaugebiete für unseren Lehm und das Ziegelwerk in Neuschoo sind über kurze Wege miteinander verbunden. Der gewonnene Ton wird oberflächennah abgebaut, da er dort die beste Qualität hat – weder zu fett noch zu mager. Durch den Abbau entstehen keine Brachflächen, sondern wertvoller Lebensraum: Überlässt man die Gebiete der Natur, bilden sich nach wenigen Jahren moorig-waldige Biotope, in denen sich Pflanzen, Frösche und Vögel niederlassen. So werden die Abbauflächen nach der Nutzung dem Artenschutz umgewidmet. Projekte, die die Ökologie der Region fördern, gehören für uns ebenso zur unternehmerischen Verantwortung wie der Bildungsauftrag. Regelmäßig versorgen wir die nahe gelegene Grundschule mit unserem Ton zum Basteln und für Besuchergruppen bieten wir Führungen durch unsere Ziegelei an.
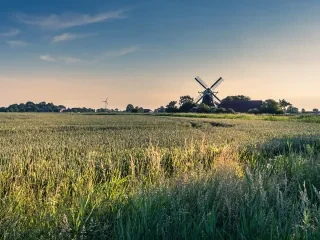
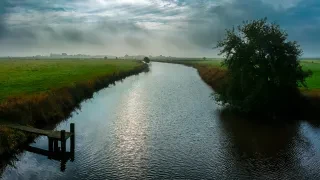
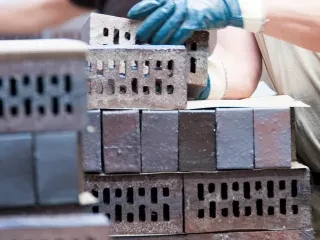
Qualität
Unsere Klinker sind echte Handarbeit.
Wittmunder Klinker erkennt man. Ihre natürliche Farbgebung entsteht komplett ohne den Einsatz von Chemikalien. Als Rohstoff verwenden wir ausschließlich unseren eigenen hochwertigen Ton, der dann bei 1200 Grad gebrannt wird. Diese Kombination aus regionalem Lehm und extrem harten Brand verhindert dauerhaft Auslaugungen und ästhetische Einbußen. Unsere Steine für die Ewigkeit gebrannt. Jeder einzelne Klinker ist von Menschenhand auf Qualität geprüft und auf Paletten sortiert. So entstehen Handsortierungen, die eine maschinelle Herstellung niemals leisten könnte. In jedem Stein steckt ein tiefes Verständnis für das Material und das altbewährte Handwerk, mit dem wir seit Generationen unseren Klinker brennen. Es ist dieses Zusammenspiel aus traditionellem Herstellungsverfahren und modernster Technologie, das unseren Klinker aus Neuschoo zum weltweiten Liebhaberprodukt macht.
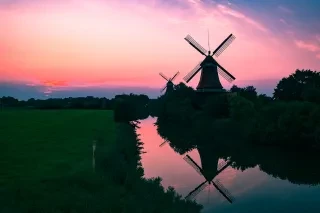
Production: Responsible production processes
In Wittmund, we don't beat about the bush: clinker bricks are fired at over 1000 degrees. But they preserve and refine the energy used in their production for an eternal life. Thanks to modern technology, the German brick industry has reduced its gas consumption by 50% over the last 30 years. In Wittmund, for example, we use the waste heat from our production to heat our buildings.
Brick manufacturers have largely exhausted their optimization potential to date and have drawn up a roadmap to climate neutrality by 2050.
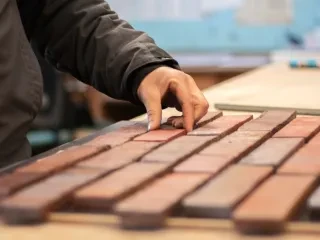
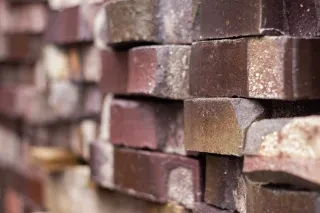
Unternehmenshistorie
Ständige Modernisierung und neue Technologien treffen auf die traditionelle Handwerkskunst und den hohen Qualitätsanspruch eines Familienbetriebs: eine Zeitreise durch mehr als 150 Jahre Wittmunder Klinker.
1860
Gründung der Königlichen Klinker-Fabrik Neuschoo durch König Georg V. von Hannover zur Versorgung der Landdrostei Aurich mit Straßenklinkern, Herstellung der Ziegel im Feldbrandverfahren
1904
Gründung der Kapitalgesellschaft Klinkerwerk Neuschoo GmbH
1906
Beginn der Industrialisierung des Werkes durch Vergrößerung und Installation einer Dampfmaschine
1912
Umstellung des Herstellungsverfahren von Feldbrand auf Deutschen Ofen, Unternehmen im alleinigen Besitz der Familie Schwarting bzw. Müller (bis heute)
1914
Umstellung auf Hoffmanschen Ringofen mit Torfbefeuerung und einer Ofenleistung von 3 Mio. Stück pro Jahr (Oldenburger Format)
1937
Zum Transport des Lehms von der Tongrube zur Ziegelei in Kipploren über Schienen löst eine Diesellok den Einsatz von Pferden ab
1951
Alle Maschinen weitestgehend elektrisch betrieben
1960
Bau von Trockenkammern
1965
Abschaffung der Diesellok und Einsatz von LKWs für den Lehmtransport
1969
Umstellung des Herstellungsverfahrens auf Tunnelofen mit Ölbefeuerung und einer Ofenleistung von 7 Mio. Stück pro Jahr (Oldenburger Format)
1978
Umstellung auf Erdgasbefeuerung
Heute
Familie Müller leitet die Klinker-Manufaktur mit ca. 40 Mitarbeitenden in vierter Generation