In the more than 150 years of its existence, we have continuously modernized the processes and technology of our manufactory, while the tried-and-tested aspects of our corporate philosophy have been retained to this day: traditional craftsmanship, a connection with the region and a high-quality and aesthetically pleasing product that is baked for eternity.
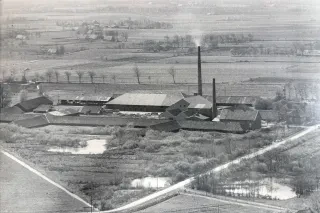
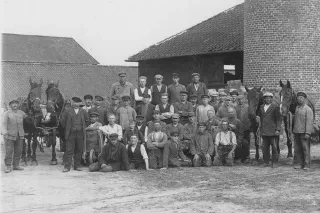
Tradition
Wittmunder Klinker has always stood for sophisticated craftsmanship with state-of-the-art technology.
The history of the brick manufactory goes back to the 19th century and is interconnected with the region. At that time, the demand for stable and durable roads increased in the agricultural region of East Frisia as a result of the industrialization. As one of the first factories that were founded in Neuschoo and the surrounding area around 150 years ago, we supplied bricks for paving roads and paths in the region. Today, we primarily burn bricks for architectural projects all over the world. Of course, our kilns have evolved as well: The first bricks were still produced using the field firing method, followed by a switch to a ring kiln system at the beginning of the 20th century. Today we fire our bricks in a state-of-the-art tunnel kiln. Times have changed – but our standards of quality and craftsmanship have remained the same.
Locality
We are rooted in the region.
Even after many decades, the basis for our bricks is still the same: the extraction areas for our clay and the manufactury in Neuschoo are connected by short distances. The clay is quarried close to the surface, as this is where it is of the best quality – neither too rich nor too lean. Quarrying does not create wasteland, but valuable habitats: if the areas are left to nature, boggy, wooded biotopes form after a few years, where plants, frogs and birds settle. In this way, the extraction areas are rededicated to species conservation after use. Projects that promote the ecology of the region are just as much a part of our corporate responsibility as our educational mission. We regularly supply the nearby elementary school with our clay for handicrafts and we offer guided tours of our manufactory for groups of visitors.
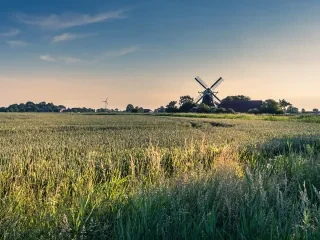
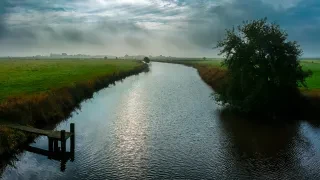
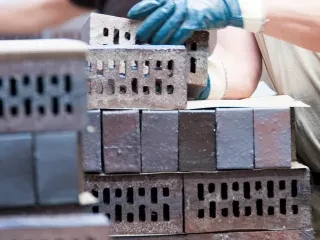
Quality
Our bricks are honest craftmenship.
You can recognize Wittmunder Klinker bricks. Their natural coloring is created completely without the use of chemicals. We only use our own high-quality clay as a raw material, which is then fired at 1200 degrees. This combination of regional clay and extremely hard firing permanently prevents leaching and aesthetic losses. Our bricks are baked for eternity. Every single brick is checked for quality and sorted onto pallets by hand. This results in manual sorting that machine production could never achieve. Each brick contains a deep understanding of the material and the time-honored craft with which we have been firing our bricks for generations. It is this combination of traditional production methods and state-of-the-art technology that makes our clinker brick from Neuschoo a favorite product worldwide.
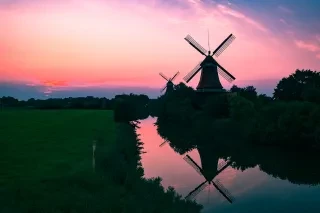
Trust
We rely on close communication and personal advice.
Over the years, our comparatively small manufactory in Neuschoo has become an insider tip among architects. Anyone planning a special project can be sure of getting exactly what they have chosen. When working together, we rely on close communication and personal advice to ensure that our customers end up with exactly the bricks they want. As all of our deliveries are hand-sorted, we not only offer a catalog of established color assortments, but also completely individual assortments on request. For renovation projects in particular, we inspect the projects ourselves on site in order to create stones that are virtually indistinguishable from the original stones. We offer architects the opportunity to get a tactile feel for our bricks: We visit the quarrying areas together, they can watch the production process and we show them how we ensure the color sorting. They are allowed to touch the bricks and create their own sorting. Thanks to this close exchange, we enjoy a high level of trust with our customers and have a deep understanding of their ideas.
Read more about the authentic refurbishment of existing facades:
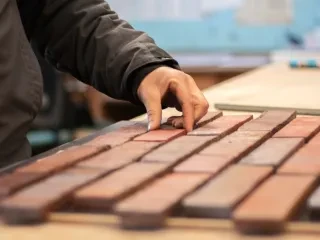
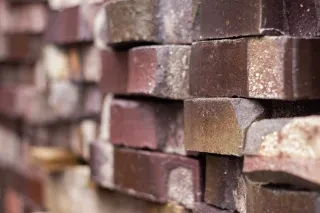
Company history
Constant modernization and new technologies meet traditional craftsmanship and the high quality standards of a family business: a journey through more than 150 years of Wittmunder Klinker.
1860
Foundation of the Royal Brick Factory Neuschoo by King Georg V of Hanover to supply the Landdrostei Aurich with street bricks, production of bricks using the field firing method
1904
Foundation of the corporation Klinkerwerk Neuschoo GmbH
1906
Start of industrialization of the factory through expansion and installation of a steam engine
1912
Conversion of the production process from field firing to German kiln, company in the sole ownership of the Schwarting and Müller families (to this day)
1914
Conversion to Hoffman's ring kiln with peat firing and a kiln capacity of 3 million pieces per year (Oldenburg format)
1937
A diesel locomotive replaces the use of horses to transport the clay from the clay pit to the brickworks in tipper wagons over rails
1951
All machines are largely electrically operated
1960
Construction of drying chambers
1965
Abolition of the diesel locomotive and use of trucks for clay transportation
1969
Conversion of the production process to tunnel kiln with oil firing and a kiln output of 7 million pieces per year (Oldenburg format)
1978
Conversion to natural gas firing
Heute
The Müller family manages the clinker brick factory with approx. 40 employees in the fourth generation